Análisis de las causas de falla por corrosión del Shell del horno en Línea Seca de ARGOS. Propuestas de soluciones.
Febrero 2018
Argos Zona Franca. Cartagena
Problema: Pérdida de masa por corrosión en el corazón del horno de la línea seca. Se evidenció afectación en un activo clave y de gran valor, se presentó corrosión bajo el aislamiento por el interior en la zona de bajas temperaturas (200°C – 420 °C) con pérdida de masa entre la cota 32 y la cota 62, sobrepasando los dos mm de espesor en algunas partes. Este problema no había sido identificado como significativo en las anteriores paradas. El estudio con ensayos de laboratorio de alto nivel de los productos de corrosión extraídos estuvo enfocado en la determinación del tipo de corrosión, sus causas y la propuesta de alternativas de soluciones.
Estudio desarrollado.
Con análisis visual y con microscopio estéreo se caracterizan las muestras y se separaron algunas de ellas para su posterior caracterización por otras técnicas: Microscopía Electrónica de Barrido (SEM-EDS), con esta técnica obtienen imágenes a partir de la topografía de la muestra así como de la composición química de la misma y con la ayuda del micro sonda EDX se realiza también microanálisis químicos elementales de la muestra; Con Micro-espectroscopia Raman se obtiene información de la composición, grupos funcionales y estructura de una muestra, también puede ser considerado como una huella digital de la muestra analizada.
Resultados.
Mediante microscopía electrónica de barrido (SEM/EDX) y espectroscopia Raman se evidenció que hubo corrosión electroquímica (húmeda) lo que no dejó de ser extraño por el rango de altas temperaturas a las que ocurre; se repitió el estudio en aquel entonces con otros residuos de corrosión, ratificándose la existencia de corrosión electroquímica en la zona de la virola donde la temperatura del tubo se movía en el intervalo de (150°C – 350 °C).
El estudio se cerró sin poder precisar ni las causas ni el mecanismo de corrosión electroquímica en dicho rango de temperaturas; sin embargo, las recomendaciones dadas en aquel entonces han permitido reducir la velocidad de corrosión en la virola.
Este fenómeno de corrosión se ha presentado en otros componentes de la planta, quedando pendiente la profundización en los mecanismos de corrosión y el desarrollo de soluciones efectivas con conocimiento preciso de las causas.
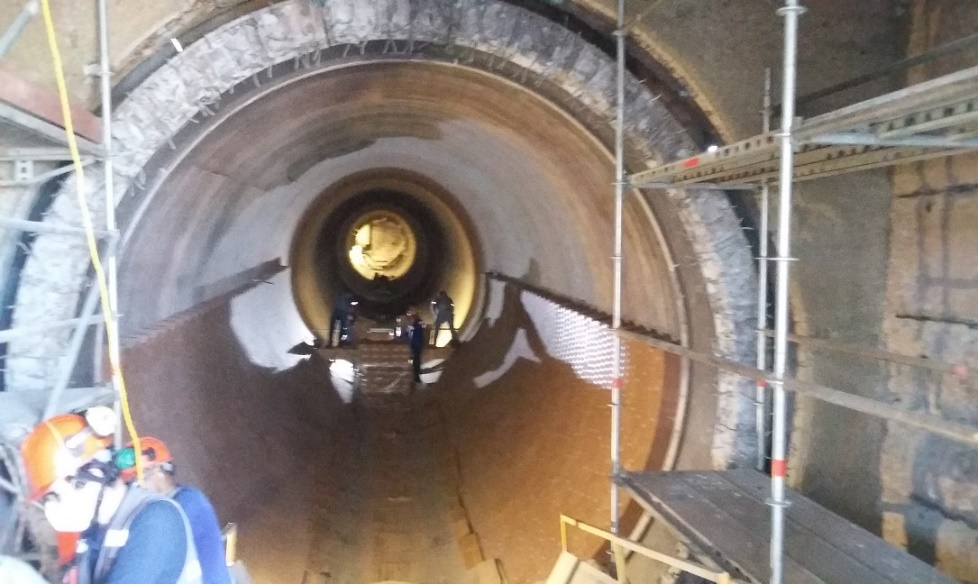
Figura 1. Vista del Shell durante la colocación del ladrillo refractario. Con limpieza no profunda. Solución de remediación con láminas de acero AISI 304 entre el tubo y el refractario.
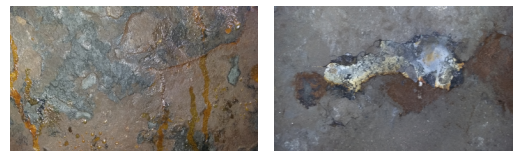
Figura 2. Superficie interior del Shell corroída: a) Antes de la extracción de cáscara corroída, b) Después de la extracción con golpes de martillo.
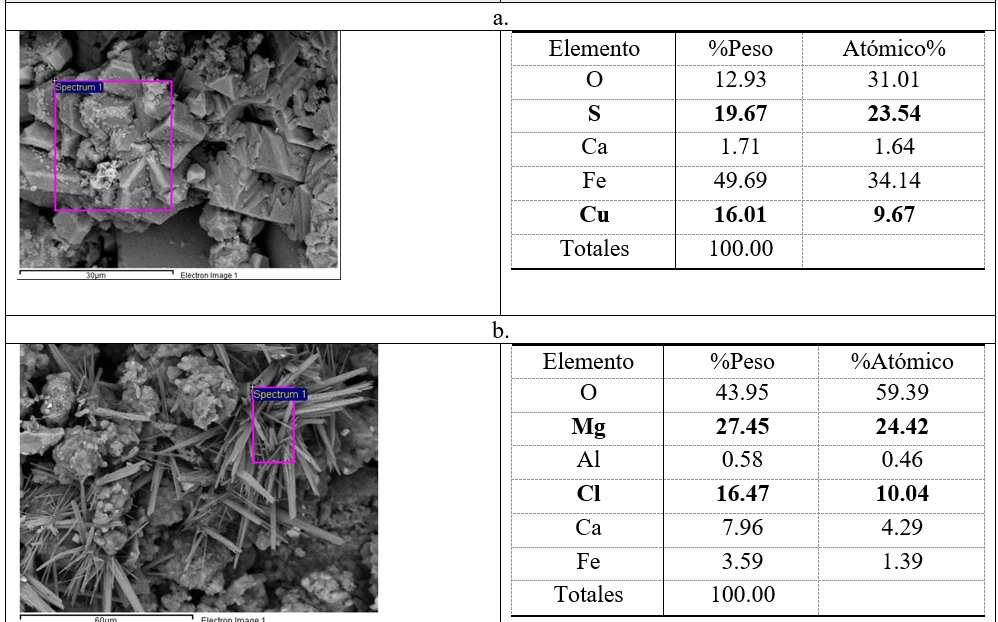
Figura 3. Análisis EDS del primer grupo de partículas